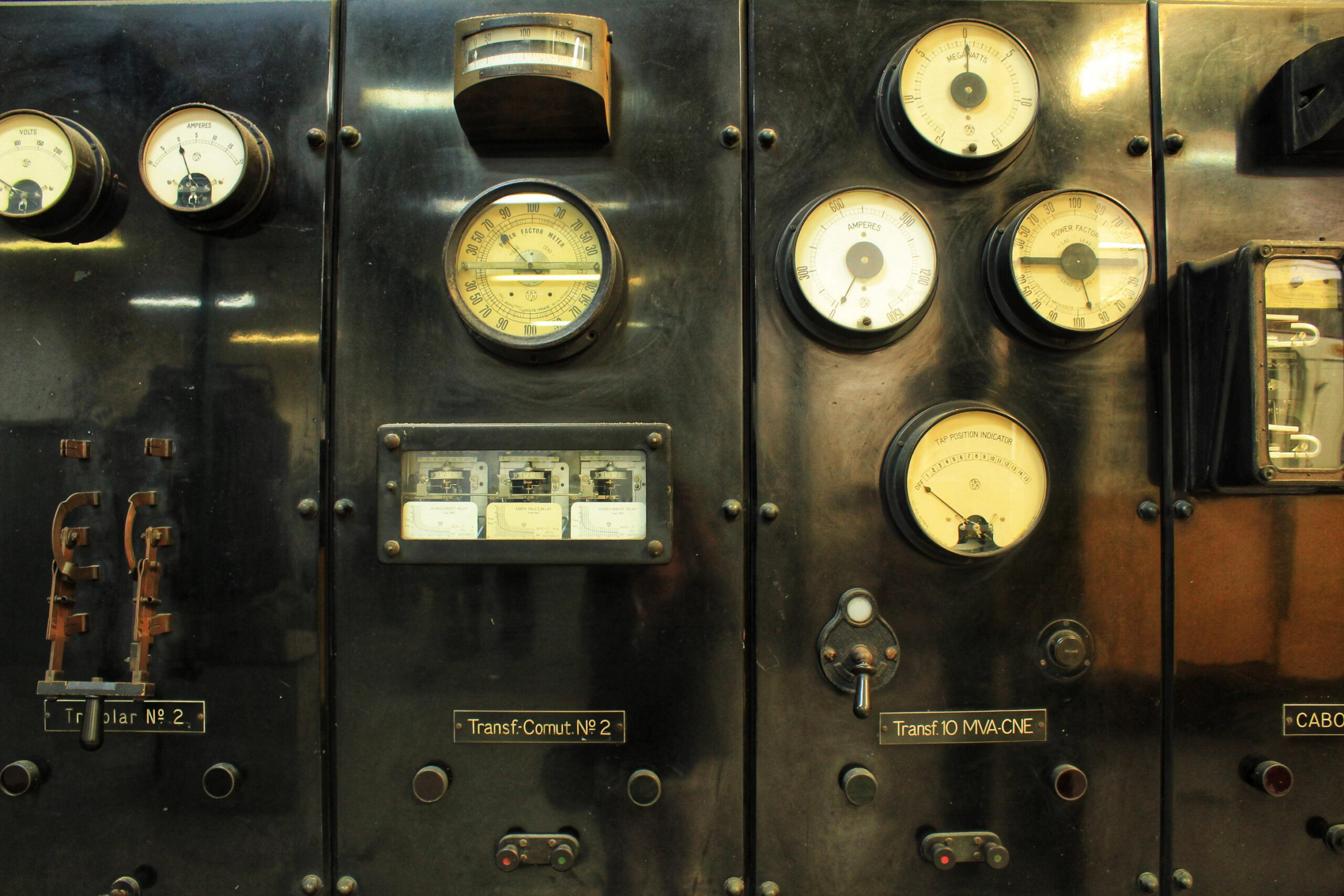
- by Todd Benadum
- May 8, 2025
- Dry Type Transformers, Padmount Transformers, Transformer Failures, Transformer Replacements
Most of the time, your transformer may seem like an inert apparatus tucked away in a cabinet. However, when energized, it is a vibrant, living thing, transforming and feeding electrical power at 60 Hertz to your facility. In addition to the metal windings and core, it contains organic materials in the form of insulation. However, like all living things, transformers age over time and eventually lose their capacity to function.
Life insurance underwriters use statistical mortality curves to estimate the chance that a person will die at a given age. Reliability engineers use a corresponding hazard curve to estimate the failure rate of a specific class of transformers as a function of their age. A stylized hazard curve, also called the bathtub curve due to its shape, is shown in Figure 1 below.
Failure Rate
Figure 1. Typical Hazard Curve for distribution transformers
The hazard curve shows that a cohort of newly installed transformers has a low positive failure rate (Infant Mortality) which declines with age as early failures are culled from the population. That is followed by a longer period of very low constant failure rates (Random Failure), until age and operating conditions begin to break down the dielectric properties of the transformer’s insulation (Wear Out Failure), after which the failure rate increases rapidly. The causes of failure are different at each stage.
Learn About ELSCO’s Repair Services
How Long Do Transformers Last?
The hazard curve shows that a cohort of newly installed transformers has a low positive failure rate (infant mortality), which declines with age as early failures are culled from the population. That is followed by a longer period of very low constant failure rates (random failure) until age and operating conditions begin to break down the dielectric properties of the transformer’s insulation and weaken its other components (Wear Out Failure), after which the failure rate increases rapidly. The causes of failure are typically different at each stage.
Infant Mortality (0-5 Years)
Premature failure is most often due to inadequate design or defects in manufacturing. Cost-cutting measures by some manufacturers lead to lower-quality conductor and insulation materials and inadequate temperature tolerances. Manufacturing defects are consequences of poor craftsmanship, substandard materials and inadequate quality control.
Automated winding and assembly processes can introduce defects and fail to detect errors in construction that lead to early failure. Mechanical failures can result from faulty construction or mishaps during transport or installation. Failures during this period are abnormal and justify an investigation to determine whether the manufacturer may be at fault.
The Elsco Advantage
ELSCO dry type transformers employ a robust thermal design using high-quality copper conductors and Nomex insulation. They are hand-wound and assembled under constant visual inspection and are tested at five stages during construction. Since 1988, we have had zero failures in operation.
ELSCO offers a five-year warranty for indoor use in a clean and dry environment on materials and workmanship for its dry type transformers. (The industry norm is one year.)
Random Failure (5-25 Years)
This is the normal operating life of a transformer during which the failure rate is the lowest. Causes of failure during this period are many and occur at random. Some are due to manufacturing defects that show up later. Others are due to abnormal operating conditions such as transient over-voltages, power surges, persistent overloading, faulty protection, environmental factors and unpredictable occurrences such as lightning strikes.
The Elsco Advantage
Although the ELSCO Warranty does not cover this time period, the robust design, quality materials and workmanship of our dry type transformers provide an extra margin of protection against the many random stressors that can cause failure as a transformer ages. We have many installed transformers in this age group and have experienced zero failures.
Additionally, we enclose our transformer coils in a specialized polyester varnish coating, isolating them from moisture and significantly reducing the risk of fire. Because our dry type designs contain no combustible liquids or coolants, they offer a more practical and safer option for potentially hazardous environments like manufacturing facilities, chemical processing plants or forestry operations.
Wear Out Failure (25+ Years)
Time and temperature are the predators of a transformer’s organic insulation materials. Long-term exposure to heat, vibration, electromagnetic and mechanical stresses within a transformer will gradually weaken the dielectric, chemical and mechanical strength of the winding insulation, and eventually there will be a breakdown and short-out, usually at a hot spot. The transformer fails (dies) and the operations depending on it are shut down.
The chances of this happening increase exponentially as an old transformer continues to get older. There comes a time when the risk and consequences of a failure are too great, and the transformer should be replaced to avoid a shutdown.
The Elsco Advantage
The insulation in ELSCO dry type transformers is the strongest in the industry. We use only DuPont Nomex® 410, with a UL rating of 220 degrees Celsius, to insulate both primary and secondary windings. Our transformers are designed for a 115-degree temperature rise over an ambient 30 degrees, which leaves a safety cushion of 75 degrees to withstand excess heat from any temporary overloading and abnormal power conditions.
Lab tests show that at a continuous temperature of 200 degrees, Nomex® 410 insulation has an expected useful life of one million hours.
Due to their robust design, quality materials and workmanship, ELSCO dry type transformers run cooler and quieter and have a longer-than-average useful life –300,000 hours or more. We have had no failures of our dry types since we began building them in 1988.
Failure Rate
Transformer Age
Determining Your Transformer’s Failure Rate
The relevant measure of age here is cumulative operating hours at load, not necessarily calendar time. The cumulative effects of time, temperature, and electrical and mechanical stresses under load determine the residual dielectric strength of insulation and the useful life of your transformer. The rate of aging will depend not only on time but on your transformer’s duty cycle and load history.
Other factors equal, a transformer with a continuous 24/7 duty cycle will age about four times as fast as one with a five-day eight-hour duty cycle. A transformer built with 180-degree (Class H) rated insulation will age faster (and fail sooner) than one with 220-degree (Class R) rated insulation. A history of unstable electric power conditions (primary voltage fluctuations, protection failure, persistent overloading, secondary power surges, shorts and switching harmonics) will increase dielectric stress, accelerate the normal aging process and shorten the useful life.
Each installation has a unique load history and the only way to accurately measure individual unit “age” is to continuously monitor and log transformer temperature and load (which we recommend.) Abnormal voltage and load events should also be recorded.
A benchmark for age measurement would be a continuous (24/7) operation at rated load, which would log a maximum of 8,760 hours of load per year. By comparison, an 8/5/50 operation would log a maximum of only 2,000 hours of load per year. No-load operations do not contribute significantly to aging.
Signs of an Aging Transformer
Even the most reliable transformers will show signs of deterioration before they fail. Identifying these warning signs early enough can help you plan ahead before a failure shuts down your operation.
- Unusual sounds: A well-functioning transformer will produce a consistent, low-humming sound. Irregular buzzing, crackling or popping noises typically indicate loose connections or failing insulation.
- Increased operating temperatures: Excessive heat rapidly breaks down the insulation and can lead to electrical shorts. If your transformer is operating hotter than normal, it could indicate deterioration internally.
- Visible deformations: Rust, corrosion, bulging components and other deformations can indicate environmental damage or internal pressure buildup. Even minor external damage can mean there’s heavy damage on the inside.
- Discoloration on windings or insulation: Look for tracking on windings, carbonization or color changes on insulation materials during inspections. These signs often indicate overheating or loose connections.
- Performance changes: Voltage fluctuations or frequent breaker trips usually occur when transformers reach the end of their service life. These signs may start out small before growing into persistent problems and failing.
- Inadequate resistance: Insufficient measurements during dielectric absorption tests suggest insulation degradation that requires immediate attention.
How Proper Maintenance Can Increase a Transformer’s Lifespan
Regular maintenance significantly extends your transformer’s service life and helps avoid unexpected failures. ELSCO Transformers recommends taking the following steps to keep your units in good working condition:
- Always de-energize your transformer before performing any hands-on maintenance. Safety must be your primary concern when working with electrical equipment.
- Establish an effective inspection schedule based on your environment and application. Perform inspections every three to six months for transformers in dusty areas. In clean, dry environments, annual checks are normally sufficient.
- Clean the dust from the cooling fans and windings with a vacuum first, followed by dry compressed air at no more than 20 to 25 psi. Avoid chemical cleaners that might damage the surface.
- Check the ventilation during every inspection and remove any obstructions if needed. If dust is problematic, consider installing filters at ventilation ports and replacing them regularly to prevent restricted airflow.
- Tighten all accessible hardware and replace any loose insulation during maintenance to prevent components from working loose during operation.
- Document all maintenance, test results and observations to track the condition of your transformer over time.
Advantages of Partnering With ELSCO Transformers
Our transformers typically last many years longer than similar products offered by competitors due to their superior designs, premium-grade materials and exceptional craftsmanship. Our skilled professionals assemble and hand-wind each unit under tight quality controls at our facility in Cincinnati, Ohio. We test each new transformer multiple times before shipping it, ensuring clients receive a dependable, high-quality product that will deliver decades of reliable service.
Our knowledgeable and professional engineers go the extra mile to understand your power needs to offer you the best possible solution. We pride ourselves on clear, honest communication throughout your purchasing and installation process. ELSCO Transformers also provides comprehensive support throughout ownership, as evident by our industry-best warranties on our new units.
If your application requires retrofitting to match your new unit with your existing connections, we can help. We’ll fabricate the necessary components and include the drawing schematics with your shipment. When your new unit arrives at your facility, you can install it into your space quickly, typically within a few hours.
During your transformer installation, our engineers will be available to answer questions and help resolve potential issues.
How We Can Help
ELSCO Transformers specializes in emergency transformer replacements, but we would rather help you prevent such a costly emergency. If you are concerned about the age and reliability of any brand of older transformer you are using, our transformer engineers can assist you. We can help you assess the risk of an imminent failure during operations and decide when a planned replacement would be economically justified.
We also offer a comprehensive range of other services to help maximize your operation’s uptime and efficiency, including transformer repairs, retrofits and custom bus work. Call 800-232-9002 or complete an online quote form today to get started.