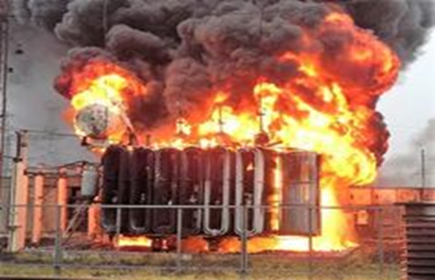
- by Todd Benadum
- May 1, 2025
- Dry Type Transformers, Padmount Transformers, Transformer Failures
Recent surveys have reported the cost of a single hour of manufacturing downtime to be anywhere between $500,000 and $5 million. The survey participants were very large, high-volume manufacturers in automated industries such as automotive, steel, chemical and pharmaceuticals. The estimates of hourly downtime costs were reported by respondents to the surveys without definitions, supporting details or analysis.
Accepting these numbers at face value for the survey population and methods employed, they are not representative of the manufacturing sector as a whole and would be a misleading benchmark for the majority of manufacturing firms that own power transformers.
In this post, we describe a simple approach to estimating the cost of a transformer failure in manufacturing based on the associated downtime and the value of lost production. Two hypothetical examples are presented with realistic calculations to illustrate the magnitude and importance of downtime cost. Any manufacturing firm could use this method to estimate the corresponding cost of a transformer failure in its own operations.
The critical cost control factor is the time to restore power after a failure and several strategies for minimizing downtime are recommended.
What Causes Transformer Failure?
Transformer failures can happen for various reasons. Depending on the operating life of a unit, different causes can affect a transformer’s reliability or even end its service life. The specific stages of failure include:
- Infant mortality: This stage covers the first five years of a transformer’s operating life. Failure during this stage typically occurs from delivery damage or manufacturing defects like poor craftsmanship, careless assembly or faulty winding during automated processes.
- Random failure: This stage covers a unit’s operating life from five years to 25 years. Typical causes of failure range from functioning in hazardous environments to experiencing consistent abnormal conditions like overloads, power surges or short circuits. This stage usually sees the least number of failures.
- Wear-out failure: Wear-out failure occurs after a transformer operates for more than 25 years. Long-time exposure to vibrations, heat and mechanical stresses will weaken the materials and structure. The insulation usually suffers the brunt of the wear.
How Much Does It Cost if Your Transformer Fails?
In manufacturing companies, the value of lost production during the downtime period is, by far, the largest component of the cost of a transformer failure. During an unscheduled power outage of a few hours or days, most costs continue but are not covered by produced value. While there are collateral costs associated with replacing a failed transformer, they are often trivial relative to the value of lost production.
To assess the hazard, it is a fair approximation to measure the downtime cost to a manufacturer as the value of lost production, which is relatively easy to measure as it is simply the calculated lost revenue. This approach also reveals the high cost of each hour of downtime. Minimizing that downtime in the event of a failure should be a high priority for manufacturing firms.
Example 1
A continuous process manufacturer operates 24/7 for 52 weeks throughout the year, with 10 days of scheduled downtime for maintenance and line changeovers. The total available production time in a year is 24 x 355 = 8520 hours per year. Assume that following a transformer failure it takes three days to find and order a suitable replacement, receive it, install it and power it up.
The resulting production downtime is 3 x 24 = 72 hours. This is 72/8520 = 0.85% of their annual production capacity, lost forever. Its monetary value depends on the value of the company’s production that relied on the failed transformer. For example:
Annual Production Value (Revenue) | Hourly Value | Downtime | Cost of a Failure |
---|---|---|---|
$100 million | $11,737 | 0.85% | $845,000 |
$500 million | $58,685 | 0.85% | $4.2 million |
$1 billion | $117,370 | 0.85% | $8.4 million |
Even if the failed transformer powered only a single step in the production line, its failure would disrupt the flow of work and soon force upstream and downstream sections to shut down. The value of lost production could be that of the entire line.
Although the chances of a 20-year-old power transformer failing are small, the financial consequences for the company can be quite large if it does. Along with lost production, there may be issues such as scrap or equipment damage incurred during the power failure, loss of customer confidence or delivery delay penalties. A continuous process manufacturer may not be able to make up for the lost production time and related costs. There are no more productive hours in the year.
Example 2
A discrete process manufacturer operates one eight-hour shift per day, five days per week for 52 weeks, with 10 holidays off. The total available production time in a year is (52 x 40) – 80 = 2,000 hours. Following a transformer failure with the same recovery time as in Example 1, the production downtime will be 40 hours, which is 2% of the company’s annual production capacity.
Its monetary value depends on the value of the company’s production that relied upon the failed transformer. For example:
Annual Production Value (Revenue) | Hourly Value | Downtime | Cost of a Failure |
---|---|---|---|
$10 million | $5,000 | 2% | $200,000 |
$50 million | $25,000 | 2% | $1 million |
$100 million | $50,000 | 2% | $2 million |
A discrete process manufacturer has more flexibility in responding to a power outage. If the transformer failure affected only part of the operations, the rest may be able to continue. Even if a failure shuts down the entire facility, the company may be able to get back on schedule through overtime work or adding a temporary second shift.
But the direct and indirect costs incurred, and profits earned during the shutdown are lost. Unanticipated cost hits of this magnitude can be catastrophic to a small or medium size company, suggesting a need for contingency planning.
In manufacturing, the critical cost factor in a transformer failure is the time it takes to restore power and resume production. A three- or even five-day recovery time is not unrealistic for a company that has not planned for a transformer failure. However, there are several ways to minimize this downtime.
How to Minimize Downtime Due to a Failed Transformer
The best way to minimize downtime and the costs that come with it is by taking a proactive approach to your power needs. The first critical step is partnering with a company that learns about your operation and helps identify the most beneficial solutions for your facility. Some of the ways we can help your company minimize the costs of transformer failure include:
Invest in Redundancy
Investing in redundant equipment and infrastructure is the most effective method. Downtime can be eliminated by installing parallel transformers. When one transformer fails, load is switched to the opposite-ended transformer. The fault is then investigated and repaired, or the offline transformer is replaced offline.
High-volume high-value continuous process manufacturers can readily justify this level of investment, and many of them have done it. But not all.
A simpler and less expensive method is to purchase backup transformers and store them on-site. Downtime then can be reduced to the time required to install, which could be anywhere from a few hours to two days depending on the availability of installation crews. This approach works well if the facility uses only a few different sizes of transformers and has adequate storage space.
Backup transformers are replaced as needed. We know of some companies that do this, but it is not a widespread practice.
Planned Replacement
A growing practice in facilities management is the planned replacement of aging electrical equipment when it approaches its useful life. The advantages of planned replacement are that it utilizes the “safe” economic life of equipment while avoiding the higher costs of catastrophic failure during operation. It is now common in overhead lighting, where the useful life is well known, and scheduled bulk replacement is more economical.
It is also used for mission-critical military electronics equipment. Except for some utilities, it has not been widely practiced for distribution transformers in the United States.
Because transformers are highly reliable devices (useful lives of 15 to 25 years with low maintenance), their operation is often taken for granted. Failures are quite rare and come as unwelcome surprises. Despite continuous reliability engineering research, the amount of publicly available data on transformer failure rates is insufficient to calculate accurate age-dependent hazard rates that would be necessary for optimum replacement planning.
As failure data and reliability research improve, planned replacement of transformers may become a more common practice.
At the unit level, the economic life of a transformer depends on the quality of materials and workmanship put into a transformer and the conditions of its use over time. As a rough rule of thumb, the maximum economic life of a power transformer under normal rated conditions is about 40 years, and any transformer older than 30 years is beginning to age physically and should be considered for replacement.
Emergency Replacement
Where redundancy is not feasible and planned replacement is not practical, the default option is to wait until a transformer fails and then replace it with some urgency. This is a common practice among small and medium-sized firms and even some large firms.
ELSCO Transformers specializes in emergency transformer replacements for dry type and padmount transformers in 500-2500 kva ratings with 4160, 12470, 13200 or 13800 primary voltages. We can usually quick-ship these sizes from stock within 24-48 hours of receiving an order, complete with custom bus work if needed.
Our “plug-and-play” installation protocol enables our replacement transformer to be installed within four hours of its arrival. The total time from receiving an order to powering up the replacement transformer would be 1.5 to 2.5 days (36 to 60 hours) including delivery. Taking the longer time of this range, ELSCO’s Emergency Transformer Replacement service would reduce the downtimes and corresponding costs of failure by half in the two examples above.
These examples show that the downtime cost savings to a manufacturer from using ELSCO’s Emergency Transformer Replacement service can easily be a multiple of $100,000.
We deliver this kind of value in emergency replacement situations by providing the following:
- 24-Hour on-call at 800-232-9002
- 95% in-stock availability of dry types and pad mounts
- Quick-ship from stock within 24-48 hours.
- Custom bus work shipped with transformer if needed.
- “plug-and-play’ installation instructions.
- A high-quality replacement transformer that will provide power efficiently and reliably for decades to come.
How to Prevent Unexpected Failures
While emergency replacement plans are crucial, preventing failures altogether provides the most cost-effective approach to protecting your operation and avoiding transformer replacement costs. Taking proactive steps early in ownership can significantly reduce the likelihood of unexpected failures and extend your transformer’s useful life.
Temperature Monitoring Systems
Temperature is one of the greatest threats to your transformer’s lifespan. Excessive heat breaks down the unit’s insulation and can damage other critical components over time. Advanced temperature monitoring systems are highly effective at mitigating these risks.
At ELSCO Transformers, we use thermocouples that help monitor temperatures where hot spots typically develop on a coil. These sensors activate cooling fans when temperatures reach a predetermined level and deactivate them after cooling.
Protection relays also help by activating alarms, initiating shutdowns or sending alerts to maintenance crews when temperatures exceed safe limits. This automation can prevent catastrophic failures during unattended hours, potentially saving hundreds of thousands of dollars in production losses and equipment damage.
Preventive Maintenance Programs
Following a practical preventive maintenance program is also helpful for preventing early failures in dry type transformers. Regular inspections can identify warning signs of deterioration long before failure occurs. We recommend following these basic steps:
- Establish inspection intervals: Base your maintenance schedule on your operating environment — every three to six months for dusty locations or annually for clean, controlled spaces.
- De-energize the transformer: Always cut power before performing any hands-on maintenance to ensure worker safety.
- Cleaning: Clean fans and windings first with a vacuum, followed by compressed air at a maximum of 20 to 25 psi. You should also avoid using chemicals that could damage the surface of your unit.
- Check for proper ventilation: Remove dust, dirt and debris that might restrict airflow.
- Visual inspections: Look for discoloration on components that could indicate an electrical problem or overheating.
- Check connections: Tighten all accessible hardware to prevent arcing, increased resistance and overheating.
- Documentation: Keeping detailed records of transformer maintenance provides valuable insight into the unit’s performance while helping predict potential failures.
Contact ELSCO Transformers Today for More Information
If you want to learn more about how ELSCO products and services can help minimize the chance of transformer failure at your facility, our team of knowledgeable and experienced engineers is ready to assist you. Besides providing a comprehensive range of medium-voltage, dry type transformers, we offer services that help increase efficiency and streamline installation, including retrofits, repairs and custom bus work. Call 800-232-9002 or request an online quote today to get started.