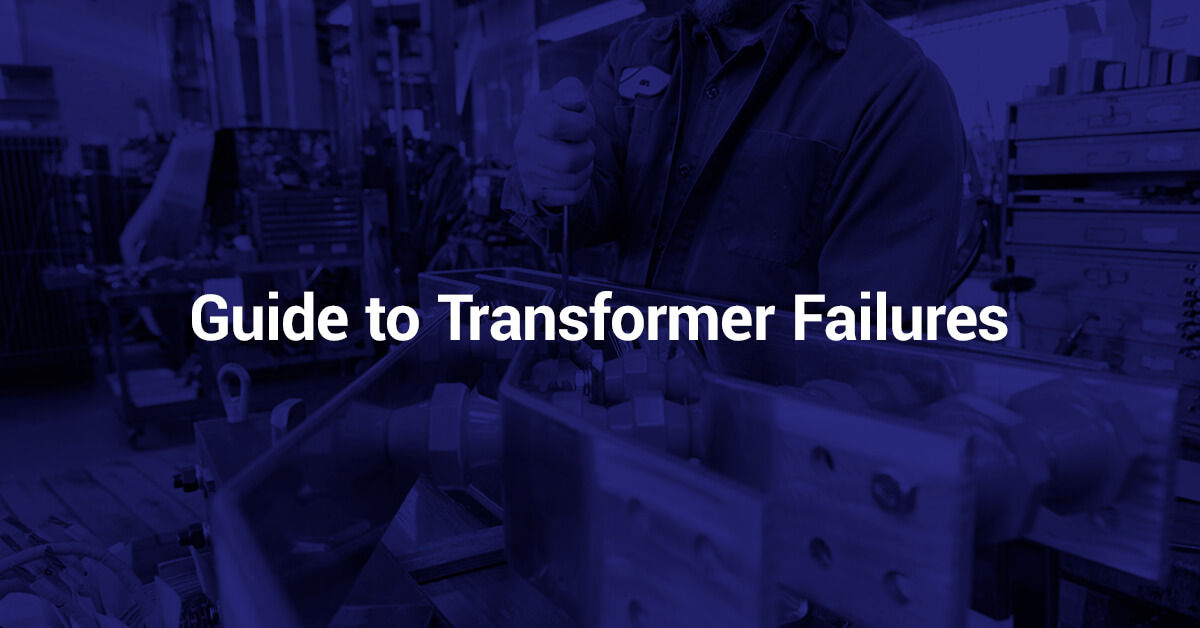
- by Todd Benadum
- September 9, 2024
- Dry Type Transformers, Padmount Transformers, Transformer Failures, Transformer Maintenance, Transformer Replacements
Transformers serve a crucial purpose as part of the power system for many facilities. Therefore, when signs of failure appear, you must quickly replace or repair the transformer to restore full operation. Knowing how to tell if your dry type will stop working or how to detect failures in an oil filled transformer will help you to schedule repairs before a catastrophic failure.
Causes of Transformer Failures
Transformer failures have a range of causes, from normal aging to improper operation. Knowing these reasons can facilitate failure prevention by avoiding some user-based causes of failure. Plus, recognizing unpredictable causes, such as natural disasters, can prompt inspections after such events occur, shortening the time your transformer isn’t functioning.
Normal Wear
Transformers will not last forever. Even with the best care, transformers have a limited life span. Therefore, the older a transformer is, the greater the likelihood the problems originated from standard wear over the years.
Age is such a strong determinant of transformer failure that a curve correlates the number of problems with the age of the system. For instance, a relatively higher number of problems early in the life span of the transformer typically happens from issues such as improper installation, operation or the wrong specs. These problems appear soon after installation when the unit’s inability to meet the facility’s needs becomes apparent due to not using a properly sized or operated unit.
Next, a lull in issues occurs as the device settles into many years of stable operation. Generally, during this middle period, normal wear does not cause a problem. However, natural disasters can cause sudden failure of the unit.
Lastly, after a decade or two or more, the transformer begins to show signs of age. The exact timing of this later period of wear causing more issues with the unit’s operation depends on the type of transformer and how well it was maintained. For instance, poorly maintained transformers that are frequently overheated may wear out prematurely due to insulation damage.
When requesting repairs, discuss the age of the transformer with the repair technician. Getting a replacement unit may improve efficiency and operation, making it a more cost-efficient option than repairing a very old model.
Natural Disasters
Natural disasters happen without warning in many parts of the country. Lightning strikes and earthquakes are common problems that lead to transformer issues. Lightning can cause electrical problems with the unit, while earthquakes can vibrate connections loose, causing short circuits. Installing lightning rods to draw away lightning can help protect transformers. In addition, vibration-reduction pads can protect against minor vibrational movement from equipment or minor temblors that typically go undetected by people. Inspecting transformers for signs of damage after earthquakes, electrical storms or other natural disasters allows for early detection of problems.
Specifications Mismatch With Needs
An early issue with transformers is when the model does not meet the capacity needs of the facility. This does not mean the transformer is at fault — the unit would likely operate properly if matched to the location’s requirements.
Another problem with specifications is not choosing the correct type of insulation. Finally, incorrectly chosen installation locations that don’t keep the unit dry and well-ventilated is another specification mismatch that can lead to premature failure of the transformer.
Facility Problems
The facility itself may have issues that prevent the transformer from operating as required. How the facility installs the transformer is crucial to how it will work. Incorrect installation may lead to failure or premature wear.
Any additional protection for the transformer must also be installed correctly. For example, lightning rods, switches and relays must have the proper setup to provide protection, monitoring and control of the transformer.
Improper Operation or Maintenance of the Transformer
As with all types of electrical devices, maintenance is essential to prolonging the life of a transformer. Inspect the unit regularly to identify growing problems before they become major concerns. Without regular maintenance, the first indication of wear may be a complete failure.
Another issue occurs with the incorrect operation of the transformer. Operating the unit with excessive loads can cause excessive wear. Incorrectly tightened connections can lead to overheating or short-circuiting. Plus, for oil filled units, allowing the oil to become contaminated can result in a damaging rise in internal temperatures.
Regular inspection and good transformer maintenance can prevent many problems caused by misuse and ensure the device’s longevity.
Types of Transformer Failure
Typically, transformer failures fall into one of two types – mechanical or electrical. These types of failures produce different symptoms and have varying causes. Regularly monitoring your transformer can identify signs of mechanical or electrical problems early.
Mechanical Failure
Mechanical failure refers to physical damage to the components of the transformer. These problems can occur for several reasons, from shipping to nearby fracking or earthquakes. Hoop failure and beam failure are common forms of mechanical problems. When you first get your transformer, conduct a sweep frequency response test and compare the results to the specifications to identify issues that may have happened during shipping.
Another way of identifying mechanical failures happens through an induction voltage test. Indications of mechanical failure from testing include partial discharge, a change in impedance and a change in the low-voltage excitation current. Often, undiagnosed mechanical problems will lead to electrical problems. Technicians only discover the mechanical issues during the examination of the causes of the electrical failure of the transformer.
Electrical Failure
Electrical failure of a transformer typically happens from damage to the insulation. This destruction may happen naturally over time. However, other causes include excessive voltage, frequent fault currents, mechanical damage to the insulation or overloads that increase degradation.
Without proper insulation, the transformer’s electrical components can overheat. A dissolved gas analysis will indicate problems with the electrical system of the transformer. Other means of identifying electrical failure may occur when an inspector notices visible damage to the insulation during an internal inspection. Other tests to conduct may include insulation power factor, winding insulation tests and winding turns ratio. Results from these will also indicate if there are any electrical issues.
Again, regularly inspecting transformers can reveal signs of electrical failure in the early stages before more severe issues.
Indications of Dry Type Transformer Failure
Dry type transformer failure has several common causes. These causes include improper use, natural disasters and normal wear. There will be some early signs to look for when you need to know how to detect failures in dry type transformers.
First, moisture inside the windings contributes to many dry type transformer failures, especially in medium voltage transformers and larger units. To detect moisture, conduct a resistance test. Use the manufacturer’s guidelines for minimum resistance readings. If the resistance reading is too low, completely dry out the transformer before conducting the test again and energizing the system.
In certain situations, such as transformers used on oil rigs, chemical contamination or salt spray can damage the transformer. For instance, exhaust from nearby engines may deposit a layer of carbon onto the coils, damaging the insulation. In addition, salt spray can corrode internal components. These problems are more likely when the ventilation for the transformer allows salt spray air or engine exhaust into the device.
Another issue comes from vibrations of heavy equipment nearby. Constant vibrations over time can loosen connections, promoting shorting or overall failure. Often, transformers that experience mechanical damage from vibrations may become noisy from the loose connections. Monitor the area for vibrations and install vibration dampening pads under the unit to mitigate this form of damage.
Lastly, poor ventilation can prevent the transformer from operating as needed. Proper airflow is necessary to provide fresh air and help maintain a stable temperature for the transformer’s operation, thus preventing overheating. Use ventilation fans for spaces that do not allow for more space to improve the natural airflow.
When it comes to how to tell if your dry type will stop working, you need to ensure that its current operating conditions are optimized. Plus, conduct regular inspections and maintenance to identify early signs of deterioration or pending failure.
Indications of Oil Filled Transformer Failure
There are several ways to tell if your oil filled transformer will stop working. Identifying these signs of potential issues starts with knowing the most common causes of oil filled transformer failure. Perhaps unsurprisingly, these types of transformers often have issues with the oil. The cooling oil used for these types of transformers may break down, reducing its ability to insulate the device.
Common problems with insulating oil used in oil filled transformers include the following:
- Low oil levels: Low oil levels, often from a leak, can lead to overheating.
- Exposure to excessive temperatures: High temperatures increase oxidation and oil breakdown.
- Contamination: Moisture in the oil is one of the most frequent sources of contamination.
- Oxidation: Oxidation causes the oil to decay more quickly.
- Corona releases: Corona releases that cause arcing can separate the oil.
- Furans: Furan analysis in the oil can predict wear.
- Static electricity: Static electricity can damage the properties of the oil that help it slow arcing and corona releases.
These oil issues can help you tell if your oil filled transformer will fail. However, the oil is not the only potential cause for failure. Other methods of detecting pending failure or the causes of a breakdown include analyzing your transformer with methods such as:
- Partial discharge: This tests the integrity of the electrical equipment.
- Frequency response: This test identifies problems with winding movements.
- Thermal modeling: This analysis compares the expected temperatures to the actual temperatures of operation.
- Dissolved gas: This can help determine whether the transformer failed and identify the cause.
If any of the above tests indicate a pending problem in an oil filled transformer, you should schedule repairs as soon as possible.
External Defects of Transformers
External defects of transformers produce problems external to the coil. Therefore, these issues happen in the tank or outside the unit. External defects may originate from problems with any of the following:
- Thermometers
- Overpressure valve or more commonly know as pressure relief device
- Cooling fans
- Loose external components
Oil filled transformers can also see Buchholz relay defects or problems with the oil level or quality.
Often problems external to the coils of the transformer occur suddenly, such as lightning strikes, earthquakes, fires or animals damaging the unit. Additional issues that may lead to external defects may include short circuits that cause an excessive current.
How to Detect External Failures
To detect external failures, regular inspection of the unit is a must. Inspections after incidents such as fires, earthquakes or lightning strikes can identify problems the natural disasters may have caused to the transformer. Plus, regular inspections can identify premature wear of the insulation or inadequate insulation based on the operational parameters.
Internal Defects of Transformers
Internal defects of transformers impact the windings or the core. Short circuits cause many of these issues. Reasons for short circuits that can damage the windings may include:
- Abnormally high load
- Electromagnetic mechanical effect
- Heat-produced deterioration
- Incorrect sizing of the surge arresters
Anything that causes a short circuit from the terminal to the core or from the winding to the grounding can damage the internal components of the transformer. Usually, the wear of the insulation causes these issues.
The winding terminals may also experience damage from lightning or excessive current. Such damage may cause the terminals to break.
Another type of internal defect, core damage usually develops very slowly over time from excessive heat reaching the core. Common causes include blockages of cooling oil in oil filled transformers or inadequate insulation around the core’s tightening screws.
How to Detect Internal Failures
Internal defects of transformers are more difficult to detect through regular inspections. Therefore, these require careful monitoring of the mechanical and electrical health of the transformer. Monitoring devices that look for mechanical internal defects connect directly to the unit. These include Buchholz relays for monitoring oil levels in oil filled transformers. Other monitoring devices include pressure rise relays and pressure relief devices.
For spotting electrical issues caused by internal failures, monitors that connect to the control cabinet can help. These devices include ground current relays, differential relays and overcurrent relays.
Contact Us at ELSCO Transformers If Your Transformer Is Failing
Failing transformers require prompt attention to prevent loss of productivity in the facility they service. If your transformer shows any signs of failure, contact us at ELSCO Transformers. We have a team of experienced engineers who can conduct repairs for a failing industrial or commercial transformer. For most major repairs, we have a 24-hour response time and do everything possible to ensure longevity from the repairs, even at maximum loads. Plus, for emergency replacement of medium voltage dry type transformers, we have a 24-hour response time and Quick Ship to get your replacement unit out to you as quickly as possible to keep your facility’s downtime minimized.