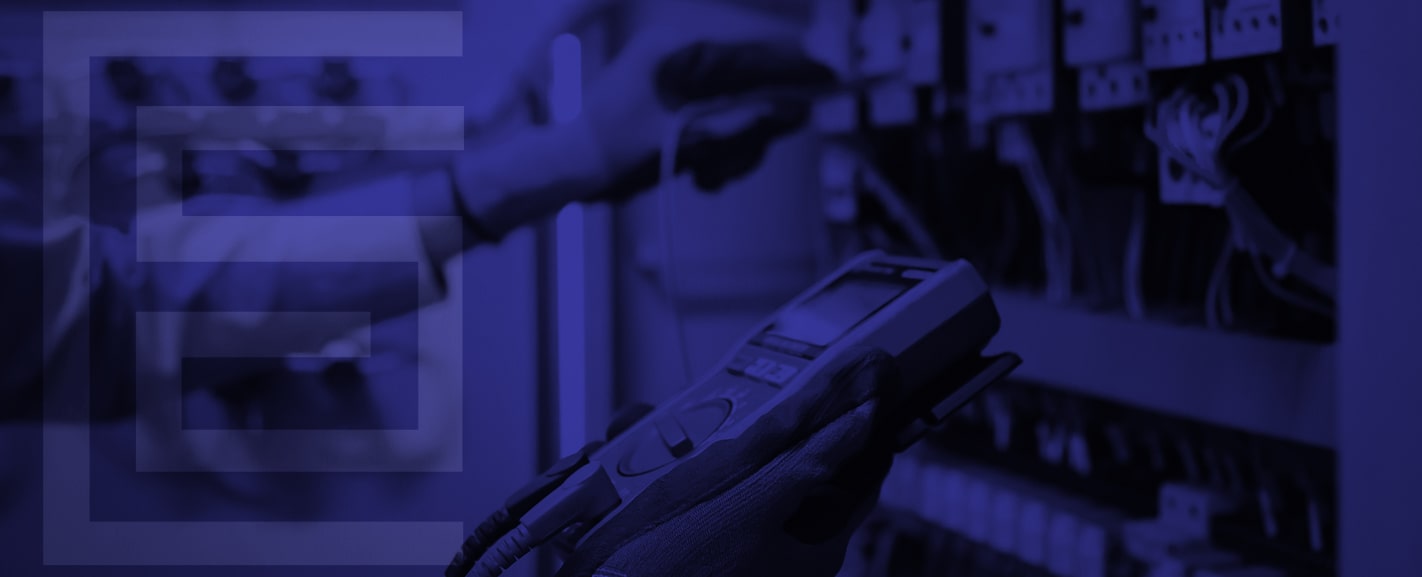
- by Todd Benadum
- April 17, 2025
- Dry Type Transformers, Padmount Transformers
Transformers are critical pieces of equipment for supplying energy to public and private buildings, from manufacturing facilities to universities and hospitals. These systems must work correctly to transform and feed electrical energy into buildings to power daily operations. Besides working correctly and safely, transformers must also use energy efficiently.
Since its founding in 1977, the U.S. Department of Energy (DOE) has regulated energy conservation standards and transformed the nation into a leader in clean energy. Along with its stringent efficiency standards for transformers, the DOE also provides regulatory testing procedures for transformers. These testing procedures appear in appendix A to subpart K of Title 10 of the Code of Federal Regulations (CFR) 431. The test procedures measure a transformer’s energy use, efficiency and estimated annual operating cost.
Transformer manufacturers must follow these DOE testing procedures for transformers to certify that their products comply with the DOE’s rules and demonstrate their transformers’ energy efficiency. The testing procedures are critical for manufacturers to communicate the efficiency of their transformers to customers. Understanding DOE energy conservation standards for transformers can help you address your transformer needs.
Test Procedure for Transformers
The general testing procedure for transformers was established on April 27, 2006, yet the DOE testing standards for transformers are adaptable. The DOE periodically requests information and public comment on whether the test procedures comply with requirements and are not unduly burdensome.
In 2017, the DOE published a request for information to collect data and information on whether to amend the procedures. Several organizations such as the American Council for an Energy-Efficient Economy, Natural Resources Defense Council and National Electrical Manufacturers Association responded with comments. The DOE amended the test procedure in 2021 to reflect these changes.
The test procedure was amended in several sections to improve consistency and accurately reflect industry standards. Some of the primary updated test procedures are as follows:
PUL Testing Requirements
A transformer’s per-unit load (PUL) is the fraction of the rated load. This specification is a critical component of the test procedure because the PUL at which the transformer is operated impacts its efficiency. The DOE defines the “standard PUL” as the PUL at which manufacturers must determine transformer efficiency to certify it to energy conservation standards. The standard PUL is the typical PUL at which most transformers operate, although some customers may operate their transformers in different conditions and at different loads.
Manufacturers must ensure 50% PUL for medium-voltage dry type transformer testing procedures and liquid-immersed transformers to comply with the energy conservation standard for transformers. Low-voltage dry type transformers are certified at a standard PUL of 35%. The industry practice is to test at 100% PUL and calculate the transformer’s efficiency based on the applicable standard PUL.
Manufacturers must only test their transformers at the standard PUL if they want to certify their efficiency. The DOE also acknowledges that a single PUL does not represent a transformer’s efficiency over the duration of its lifetime. In the past, the DOE considered a multiple-PUL weighted-average efficiency metric to more accurately reflect how transformers operate but determined that such a rule would impose an undue burden on manufacturers.
Manufacturers may also choose to make voluntary representations at additional PULs. Manufacturers can represent efficiency, load loss and no-load loss at these additional PULs using the testing procedure. This allowance provides more information to customers who may operate their transformers at different installation conditions than the ones outlined in the energy conservation standard.
Temperature Correction
Another aspect of the DOE testing standards for transformers is the reference temperature at which the manufacturer determines the transformer energy losses. Reference temperatures provide a common reference point for efficiency comparison.
Manufacturers must use the applicable reference temperature when performing test procedures for their transformers depending on their transformer category:
- Medium-voltage dry type: The reference temperature must be 20 degrees Celsius for no-load loss and 75 degrees for load loss.
- Low-voltage dry type: The reference temperature is 20 degrees Celsius for no-load loss and 75 degrees for load loss.
- Liquid-immersed: The reference temperature is 20 degrees Celsius for no-load loss and 55 degrees for load loss.
The current testing procedures for transformers require manufacturers to correct losses to the reference temperature if they perform the testing procedure under a different temperature. This process is temperature correction, which involves calculating a transformer’s losses as though its internal temperature was the reference temperature.
Manufacturers may also make voluntary representations at an additional reference temperature to provide customers with further information on which to decide which transformer to install.
Test Frequency
Another critical aspect of DOE testing procedures for transformers is test frequency. The test frequency is the frequency of electrical power supplied to the transformer during the test procedure. Both no-load loss and load-loss tests must be performed under a specific test frequency.
In a 2019 notice of proposed rulemaking, the DOE proposed requiring test procedures to be performed at 60 hertz. Previously, the testing procedure was required to occur at the rated frequency, which was not explicitly defined.
The amended requirements specify that the testing procedure must only occur at a frequency of 60 hertz, which aligns with the definition of a distribution transformer outlined in 10 CFR 431.192.
Test Equipment Calibration
Testing procedures for transformers involve finding a range of measurements, including:
- Winding temperature
- Direct current resistance of the transformer windings
- Transformer losses
These tests all require sophisticated measurement equipment, such as:
- Ammeters
- Voltmeters
- Wattmeters
- Thermocouples
- Other temperature-sensing devices
Each type of test equipment must function properly to provide accurate test procedure results. For example, measuring instruments used in voltmeter-ammeter circuits must be sensitive enough to detect at least a 0.1% change in winding resistance.
The DOE has specified additional requirements for certifying and calibrating test equipment to ensure it performs as expected. Manufacturers must routinely calibrate their test instruments and perform quality assurance procedures before performing tests. Manufacturers must also maintain thorough calibration records.
Choose Medium-Voltage Transformers From ELSCO Transformers
Although DOE testing procedures for transformers are extensive, they enable consumers to understand transformer energy efficiency and benefit the industry. Ensuring your transformers follow DOE testing procedures provides reliable, efficient units.
If you need highly efficient transformers that comply with DOE regulations, ELSCO Transformers can help. ELSCO stocks high-quality medium-voltage dry type and padmount transformers to support a wide range of industries. Our dry type transformers meet or exceed DOE efficiency standards, and our new transformers come with a five-year warranty. We also offer services like transformer retrofits and transformer repairs when you need to ensure your transformer will perform at maximum capacity.
To learn more about our products, request a quote today.