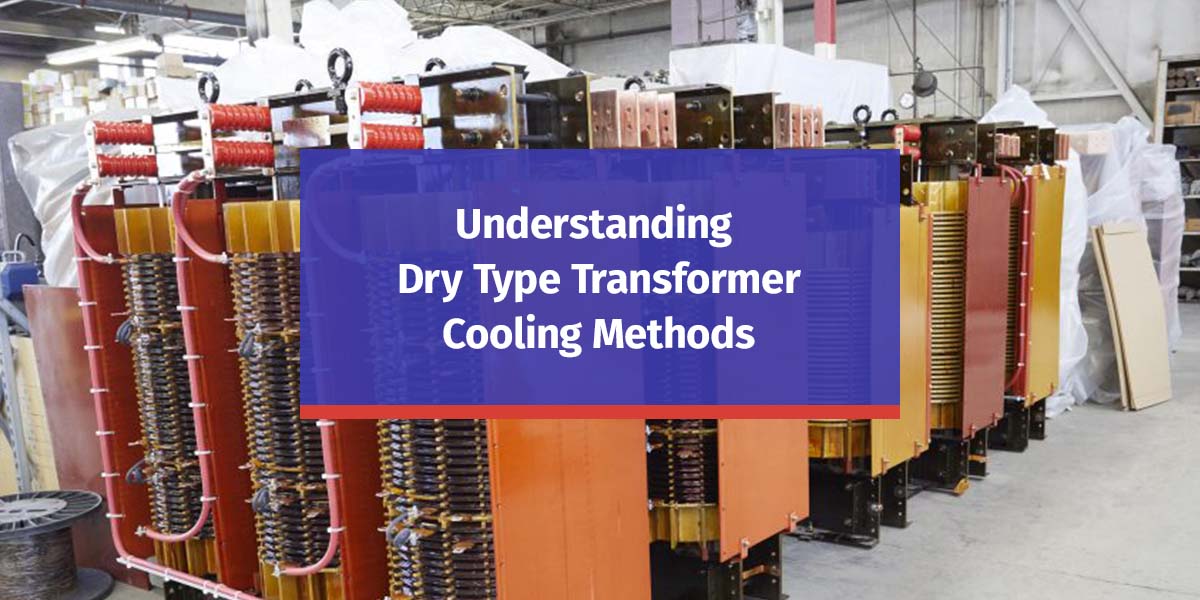
- by Todd Benadum
- August 23, 2024
- Dry Type Transformers, Transformer Build Process
Dry type transformers reduce conventional power circuit voltage. This action generates copious amounts of heat by transferring energy between alternating-current circuits, which demands cooling techniques. Keeping transformers at moderate temperatures preserves their integrity, helping them stay functional for longer.
Various techniques keep these transformers cool, each suiting different applications. Understanding dry type cooling methods is crucial for ensuring transformers perform optimally, stay safe and reduce energy losses.
Understanding Dry Type Transformers
A dry type transformer uses bus work to conduct energy. It has high voltage on one side and low voltage on the other, using air cooling methods to dissipate heat from cooling ducts, drawing cool air from bottom vents and pushing hot air out through top vents. The transformer uses air instead of liquid for cooling and solid insulation materials like resin or epoxy.
Key features of these transformers include:
- Safety: Because they do not contain flammable liquids, these transformers are safer to use, pose less fire risk and have a lower environmental impact.
- Versatility: Dry type transformers are used in indoor settings like hospitals, schools and commercial buildings because they do not emit harmful gases and are quiet. Any outdoor installations must be protected in a certified enclosure and used only in moderate heat and humidity conditions.
Dry Type Transformer Cooling Methods
Transformer cooling happens both inside and outside the device. Internal cooling focuses on the natural tendency for heat to dissipate to areas of lower temperature without any active interference, while external cooling actively forces heat out of the transformer enclosure.
Two common methods used for dry type transformers are natural air cooling and forced air cooling:
Natural Air Cooling
When a transformer uses natural air cooling (AA), it relies on natural air circulation to remove air from its surface. The design lets heat escape into the surrounding air without using fans or pumps. It is a simple, commonly used method.
As the transformer operates, heat is generated from electrical losses in the core and windings. As this heat warms the air surrounding the transformer, it loses density and creates a natural convection current. While this warm air rises, cooler air from the surroundings moves in to replace it, creating an ongoing cycle of air movement around the transformer. The air movement is completely natural and needs no additional mechanical systems to dissipate warm air.
The transformer often sits in a well-ventilated area with steady airflow. This method is simple and reliable, with no moving parts at risk of breaking down, so it requires minimal maintenance. It is quiet and best for transformers with low ratings.
Natural air cooling is well suited for applications requiring lower voltages and amperages, including:
- Industrial and commercial applications
- Offices
- Indoor substations
Forced Air Cooling
Forced air cooling (FA) uses fans or blowers to blow air over the transformer coils. It enhances cooling, making it an efficient method of handling higher loads in transformers. FA is effective in a variety of environments, but surrounding air quality and ambient temperatures should be moderate to keep the cooling system functioning optimally.
The fans in this cooling method can be axial or centrifugal, depending on space constraints and design requirements. As air pushes through the transformer core and windings, heat disperses. This flow can be directed vertically or horizontally and, in some designs, may include channels or ducts to guide airflow more efficiently.
These systems often use temperature sensors that monitor the transformer in real time. They can connect to the control system that regulates the fans and activate when the transformer temperature exceeds a specific threshold. In this way, sensors optimize energy use and reduce unnecessary wear on the fans. Integrating sensors with supervisory control and data acquisition systems allows for real time data relay and remote monitoring with analysis of the transformer’s temperature trends.
Forced air cooling is well suited for more demanding industries and applications, such as:
- Industrial facilities
- Urban substations
- Commercial buildings
- Renewable energy installations
- Critical infrastructure
Comparison and Selection Considerations
When comparing dry type transformer cooling methods, consider how well each method dissipates heat, which is crucial for transformer performance. Different methods also produce varying noise levels. Where noise is a concern, opt for a quieter method. Finally, ensure the transformer design and cooling method are compatible.
Cooling Method | Description | Advantages | Disadvantages |
Natural Air Cooling | Uses natural air circulation to dissipate heat. | Simple, cost-effective, no moving parts.Less risk of mechanical failure, as there are no mechanical parts.Quiet operation as natural air cooling operates silently. | Limited cooling capacity.Not suited for hot climates or confined spaces with poor ventilation.Not suited for larger transformers or those with higher power ratings. |
Forced Air Cooling | Uses blowers or fans to push air over the transformer coils. | Very efficient, suitable for higher loads.Extends transformer life span.Using temperature sensors allows for the precise cooling process management. | Increased energy consumption from fans. Mechanical parts like fans require routine maintenance.Fans and blowers increase noise levels. |
Why Trust Us
ELSCO Transformers builds transformers from superior-grade materials to help you spend less on maintenance and services. Our team has decades of combined experience working with transformers, giving you access to specialized knowledge and custom services.
Since we began creating our own dry type transformers in 1988, we have had zero product failures due to our high-quality designs, materials and craftsmanship. All of our dry type transformers come with a five-year warranty against workmanship defects, so you can trust in our expertise and the quality of our equipment.
We also offer the following benefits:
- Longevity: Expect a 30-year service life from our dry type units. They are heat- and short-circuit-resistant, significantly lowering their risk of premature failure.
- Easy installation: We can replace old, broken transformers with a custom plug-and-play retrofit device, reducing waiting times.
- Adverse environment suitability: Our transformers feature moisture core and coil protection, making them suitable for most indoor environments, even in areas with seismic activity.
Browse Dry Type Transformers From ELSCO Transformers
Dry type transformer cooling methods help maintain the longevity and performance of transformers that use air instead of liquid for cooling and insulation. No matter how you plan to cool your dry type transformer, ensure you select a transformer that meets your operational needs and uses only the best quality materials.
At ELSCO Transformers, emergency transformer replacements are our specialty. We offer 500 to 2,500 kVA range transformers with voltage options of 2400, 4160, 12470, 13200 and 13800. You can also make use of our custom bus work and retrofitting options to ensure our units work with your existing setup.
Enjoy a fast turnaround time with our Quick Ship option and a range of other services. Browse our ready-to-ship dry type transformer selection today.