- by Todd Benadum
- December 26, 2023
- Dry Type Transformers
More than 40% of the energy used in the United States is consumed by building operations, including the electrical equipment and appliances within those buildings. While this equipment is essential to daily functionality in homes and business locations, ensuring that these appliances use energy efficiently is also gaining importance.
Since the Energy Policy and Conservation Act of 1975 was amended, the U.S. Department of Energy (DOE) has been responsible for ensuring that appliances meet a minimum standard of energy and water efficiency. The DOE rules apply to over 60 different product types used in public and commercial applications, including transformers.
Distribution transformers play a significant role in daily life, transforming the final voltage in an electric power distribution system. Transformers convert power into a form usable within buildings, making it essential for public, commercial and industrial applications. Since 2007, the Department of Energy has played a role in regulating the efficiency of transformers, and they’ve regularly updated their standards every several years.
The most recent updates are from 2016, deployed with efficiency and consumer benefits in mind. In December 2022, the DOE proposed a new set of energy-efficiency requirements for distribution transformers that, if approved, should take effect in 2027. However, a rule proposed in January 2023 could affect the 2027 regulations. This proposed rule has bipartisan support and, if approved, would halt the 2027 regulations or involve a slower phase-in of the policies.
Transformer Efficiency
The power efficiency of a transformer is defined as1
Efficiency = Power Used / Power Supplied = L x (KVA rating) x PF / L x (KVA rating) x PF + total losses
where L is the fraction of rated load, PF is the power factor, and total losses include no-load and load losses due to resistance, inductance and stray flux losses within the transformer.
Transformer efficiency depends critically on design, materials and construction, and is important because the power user pays for the power supplied, which includes the power losses dissipated by heat.
Department of Energy (DOE) Efficiency
Pursuant to the Energy Act of 2005, the US Department of Energy (DOE) has regulated the efficiency of medium-voltage transformers since 2007. Manufacturers are required to measure the efficiency of their new transformers and certify them to be in compliance with the DOE efficiency standards prior to shipment.
The current DOE efficiency standards applicable to ELSCO dry type transformers are shown in Table 1.
Table 1. DOE Minimum Efficiency Standards for ELSCO Three-phase Medium Voltage Dry Type Transformers (DOE-2016 CFR 434.196; 45 – 95kv BIL)2
KVA | Efficiency (%) |
---|---|
500 | 98.99 |
750 | 99.12 |
1000 | 99.20 |
1500 | 99.30 |
2000 | 99.36 |
2500 | 99.41 |
ELSCO performs the DOE efficiency test on all new transformers before they are shipped, and certifies that they are no less than the minimum efficiency standard for their KVA rating.
The DOE also regulates the test procedures that manufacturers must use to measure and certify efficiency. The DOE mandated test is a highly standardized test designed to make efficiency measurements comparable between transformers with the same KVA rating produced by different manufacturers.
The DOE efficiency test regulations for medium-voltage dry-type transformers require strict adherence to the following conditions:3
Measurement of losses must be made at:
- 50% of rated load of the transformer (L = 0.5) )
- Power factor (PF) equals 1
- Coil temperatures of 20°C for no-load losses and 75°C for load losses
- Excitation at rated voltages, with pure sinusoidal waveform at 60 Herz.
Accuracy tolerances are prescribed for each of these conditions in the regulations, and any out-of- tolerance conditions must be corrected for when DOE efficiency is calculated.
Because this is a highly standardized certification test, the resulting DOE efficiency measure is only an approximate estimate of the power efficiency of the transformer in actual operation because the standard conditions of the DOE test cannot be controlled. Depending on the operating conditions, the measured power efficiency of an ELSCO transformer in operation may be significantly different from its certified DOE efficiency. That possibility is acknowledged by the DOE.
Operating Efficiency Characteristics of ELSCO Dry Type Transformers
Operating Efficiency
The operating efficiency of an installed transformer can be measured and recorded by permanent power meters installed on the primary and secondary terminals of the transformer, or by performing an energy audit using portable instruments. Transformer efficiency is easiest to calculate when the load is fairly constant and continuous over long periods of time. When the load is highly variable over a span of a few hours or the duty cycle is intermittent, a time-weighted average should be calculated f rom several measurements taken at different loads.
The efficiency measured under operating conditions may be somewhat lower than the certified DOE efficiency. The operating conditions most likely to affect this are:
- Load and duty cycle
- Power factor
- Current waveform
- Coil temperature
The operating efficiency of your ELSCO transformer will be determined by the combined effects of its load factor, duty cycle, power factor and temperature while it is in operation.
Learn More About Our Dry Type Transformers
Variations from 50% of Rated Load
The effect of load on transformer efficiency can be estimated using the same DOE testing software used to make error corrections. The relationship between DOE efficiency and percent of rated load for ELSCO dry type transformers, with all other conditions in DOE test compliance, is shown in Figure 1.
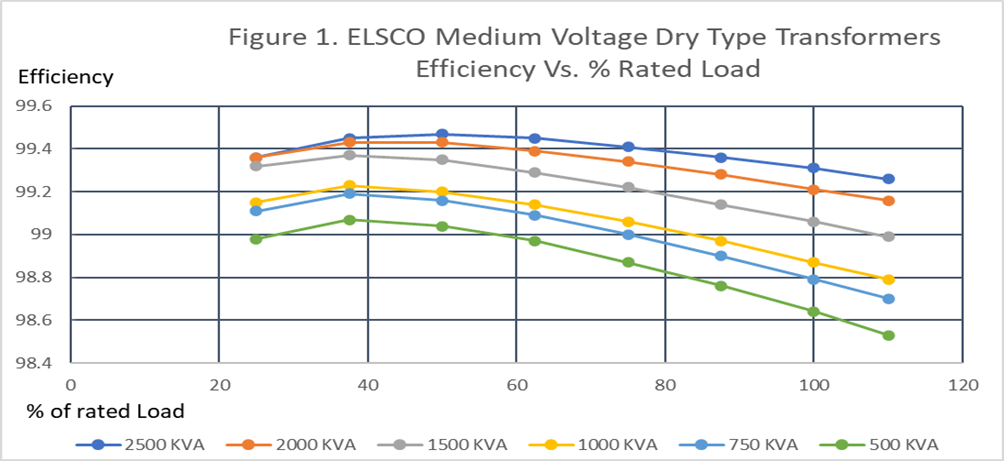
All of these transformers meet the minimum DOE efficiency standards at 50% of rated load, and in fact would be in compliance with the standards everywhere on their respective plots.
The “sweet spots” for high efficiency are in the range of 40% to 75% of rated load for the 2000 KVA and 2500 KVA units, and 30% to 50% of rated load for the 500 KVA to 1500 KVA units. Note that efficiency falls off rapidly when the load is below 40% or above 80% of the transformer rating.
Every transformer application has its own load demand and duty cycle which can be quite variable over time. Even when a transformer can supply a dynamic load demand, continuous operating loads below 30% or above 80% of the transformer rating will be relatively inefficient. Ideally, the range of dynamic load fluctuations should fall within the “sweet zone” of your transformer. Older transformers operating at 80% of their rating or higher may be a candidate for an upgraded replacement.
Power Factor and Current Waveform
The power factor of an AC power system is defined as the ratio of the real power absorbed by the load to the apparent power flowing in the circuit.3 A power factor less than 1 indicates that the voltage and current are not in phase (displacement factor loss ) or the sinusoidal wave form is distorted. (distortion power factor loss), reducing the real power absorbed. These power factor losses are inherent in the electrical properties of the load, and while not directly attributable to the supplying transformer they will affect the measurement of power efficiency.
- Purely resistive AC loads (incandescent lamps or heating elements) do not shift phase and have a power factor close to 1, but usually make up a small fraction of industrial loads.
- Reactive loads (capacitors and inductors such as motors, transformers, solenoids, relays, fluorescent lamp ballasts and others) will shift phase and have a power factor well below 1. These are typical of industrial loads.
- Non-linear loads (rectifiers, electric welding machines, arc furnaces and other switching devices such as switched-mode low voltage DC power supplies) also distort the sinusoidal waveform and may have a power factor much less than 1. These waveform distortions also generate harmonic currents to the 60 Herz frequency which will increase eddy current losses in a transformer.
The total power factor of the system is the product of the resistive, displacement and distortion factors. Most commercial and industrial transformer users have a mix of resistive, reactive and non-linear loads and will experience a power factor less than 1.
Calculations using the DOE software indicate that, for an ELSCO 1500 KVA dry type transformer, each 1% decrease in power factor results in about a .01% loss in transformer efficiency. For higher KVA rated units the efficiency loss rates are slightly less, and for lower KVA rated units the loss rates are slightly more.
For example, an ELSCO 1500 KVA 3-phase transformer operating a continuous 750 KVA load with a power factor of 0.90 will have power factor losses of 0.1%, which will accumulate to 6000 KWH over 8000 hours of operation.
Some utilities charge higher rates to commercial and industrial customers who have a power factor below some limit, typically 0.9 to 0.95.3 Power-factor correction circuits can be installed to bring the power factor close to 1, but the economics of this depends on the amount and value of power factor loss and the cost of correction.
Coil Temperatures
The DOE test condition of a 20°C (68°F) coil temperature at no load will likely be exceeded unless the transformer is in an enclosed air conditioned space. The DOE test condition of a 75°C coil temperature at 50% of rated load may also be exceeded by an ELSCO transformer designed for a 115°C temperature ruse if the ambient temperature of the transformer space exceeds 40°C .
A dry type transformer typically loses about 1% of its capacity for each 1°C increase in ambient temperature above 30°C5,6,. Transformer efficiency declines slightly with increasing temperature even at a fixed load, because the higher temperature increases resistance of the copper coils. An increase in coil temperature with a static fixed load could be caused by a large increase in ambient temperature, degradation of the HVAC system. or a hot spot getting hotter, and should be investigated.
The most important relationship between coil temperature and transformer efficiency is associated with load losses. Energy losses in the form of heat are proportional to the square of the current, or load. (That relationship is what causes a reduction in efficiency at load factors higher than 50%.) Heat is a byproduct of inefficiency but can also contribute to it. If the rate of dissipation of heat by natural or convective air flow is constant, the temperature of the coils will rise. This can be mitigated by regulating the temperature and air flow of the transformer space at a small energy cost.
ELSCO dry type transformers use Class 220 insulation over copper windings and are designed for a 115°C temperature rise at full rated load. Due to their quality design, materials and construction, they run cooler and quieter than most alternative products on the market and contain a 50°C safety margin for temperature rise. Providing adequate cooling air flow and temperature will help to maintain high operational efficiency and prolong the useful life of your transformer.
Contact ELSCO Transformers Today
The operating efficiency of your ELSCO dry type transformer depends not only on its DOE efficiency rating, but also on the dynamic electrical properties of the load it serves. Transformer efficiency measured in operation will usually be less than its certified DOE efficiency.
Whatever your load requirements, you can be assured that an ELSCO dry type transformer meets or exceeds the minimum DOE efficiency standard for its rating, and will provide highly efficient and reliable power for a useful life of 35 years or more. We offer a five-year warranty on materials and workmanship on new dry type transformers and have never had a warranty claim.
To learn how ELSCO designs and builds highly efficient and reliable dry type transformers or to talk with one of our transformer engineers about the efficiency of your transformer, Call 800-232- 9200.
References
- Harlow, James, H., Electric Power Transformer Engineering, 3rd ed 2012.; Chap 2, Power Transformers, p.2-6
- Energy Conservation Standards and their Effective Dates, Code of Federal Regulations (CFR) Section 431.196.
- Uniform Test Method for Measuring the Energy Consumption of Distribution Transformers, CFR 431, Appendix A to Subpart K
- www.wikipedia.org/wiki/power-factor
- Fink, D. G, & Beaty, H. W., Standard Handbook for Electrical Engineers, 13th ed.1993; Chap. 10, Table 10-7, p. 10-62
- Ishak, M. T, Zhong, Q., Wang, D, Impact of Load Profiles, WTI Setting and Hotspot Factors on Loss-of-Life of Dual Cooling Mode Transformers, Proceedings of the 16th International Symposium on High Voltage Engineering, SAIEEE 2009, ISBN 978-0-620-44584-9, Paper F-31, pp 1-5.
- www.wikimedia.org/wiki/copper-resistivity
- “Images for Sinusoidal Waveforms in AC Circuits” (Google search)